آب شیرین کن صنعتی سیستمی است کامل با ورودی آب خوراک و لوله های تخلیه مجزا برای کنسانتره است.شاخص های مدنظر مانند میزان نگه دارندگی نمک و فشار در آب ورودی و خروجی باید آنالیز و با هم مقایسه شوند.
هدف طراح سیستم اسمز معکوس وجود کمترین فشار غشا و صرفه جویی در هزینه نصب و حداکثر کارایی خواهد بود.
نمک زدایی برای آب شور در آب شیرین کن صنعتی حدود ۸۵ درصد است. این بستگی به حلالیت جامدات معلق موجود در آب دارد. در طول نمک زدایی آب دریا، بازیابی چهل تا پنجاه درصد مطلوب است. نمک زدایی آب دریا به فشار اسمزی ,آب خوراک و انواع غشای اعمال شده بستگی دارد.
فناوری آب شیرین کن
بخوانید
روند مستمر
در آب شیرین کن ها یک سیستم فیلتراسیون غشایی معمولاً برای حضور در یک فرآیند مداوم طراحی می شود. این فرایند می تواند به شکل پیوسته طراحی شود. شرایط فرآیند مانند جریان آب تغذیه و جریان نفوذ، پیوسته هستند.
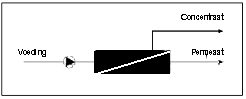
بیشتر بخوانید: https://www.lenntech.com/desalination-installations-system-design.htm#ixzz7blqQRSgW
در مورد سیستم های اسمز معکوس نیز همینطور است. اینها همچنین برای حضور در یک فرآیند پیوسته با جریان نفوذ مداوم و بازیابی سیستم که ثابت است طراحی شدهاند.
تغییرات دمای آب و درجه رسوب آب تغذیه با تنظیم فشار تغذیه جبران می شود.
سیستم چند مرحله ای در آب شیرین کن
سیستم هایی که از بیش از یک مرحله تشکیل شده اند سیستم های چند مرحله ای نامیده می شوند. این سیستمها میتوانند بازدهی بهتری داشته باشند، بدون اینکه از محدودیتهای بازیابی یک عنصر تجاوز کنند. برای به دست آوردن بازیابی تا ۷۰٪، باید دو مرحله در سیستم تصفیه آب خوراک اجرا شود.
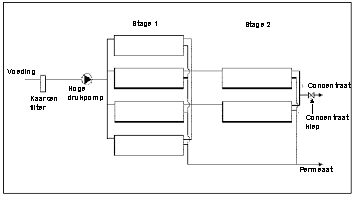
هنگامی که بازدهی بالاتر مد نظر است، عناصر غشایی بیشتری باید به صورت سری متصل شوند. یک سیستم معمولی دو مرحله ای از نسبت مرحله ۲:۱ برای نمک زدایی آب دریا با محتوای جامدات محلول بالا استفاده می کند.
جریان برق و کنسانتره گردش مجدد
مفهوم جریان پلاگین طراحی استاندارد سیستم اسمز معکوس برای کاربردهای نمک زدایی آب است.
آب تغذیه تنها یک بار از طریق یک سیستم جریان برقی عبور داده می شود. کسری از آب خوراک از یک غشاء عبور می کند تا تراوش کند. مابقی آب خوراک از نمک حاصل نمی شود و بیشتر و بیشتر غلیظ می شود.
هنگامی که تعداد عناصر غشایی در یک سیستم جریان پلاگین برای دستیابی به بازیابی سیستم کم باشد، گردش مجدد کنسانتره ممکن است دخیل باشد. در طول چرخش مجدد، بخشی از کنسانتره به سمت آب تغذیه ماژول هدایت می شود. کنسانتره بازیافتی با آب خوراک مخلوط می شود و یک بار دیگر تصفیه می شود
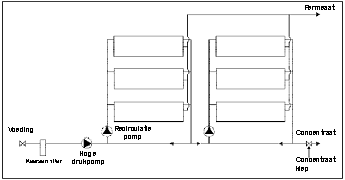
تعداد عناصر موجود در هر مخزن تحت فشار
سیستم های اسمز معکوس معمولاً برای یک جریان نفوذ خاص طراحی می شوند. برای رسیدن به این جریان، تعدادی عنصر پوسته مورد نیاز است. تعداد عناصر غشایی که در محل نصب قرار می گیرند. به شار طراحی شده بستگی دارد.
برای نمک زدایی آب دریا عامل محدود کننده حداکثر فشار ممکن است از ۶۹ بار تجاوز نکند.
فشار آب تغذیه
با توجه به طراحی سیستم، فشار تغذیه خاصی مورد نیاز است. شار، اتلاف انرژی در سیستم و فشار اسمزی فشار تغذیه مورد نیاز سیستم را تعیین می کند. پمپ تغذیه ای که جریانی بالاتر از جریانی که از نظر تئوری مورد نیاز است را امکان پذیر می کند، فشار تغذیه را مداوم نگه می دارد. پمپ تغذیه ای که فشار تغذیه را ۲۵ درصد افزایش دهد در عمل رضایت بخش خواهد بود.
هنگامی که سیستم راه اندازی می شود، وضعیت اولیه ثبت می شود. تمام پارامترهای مربوطه باید در یک گزارش ثبت و یادداشت شوند. بر اساس این داده ها، عملکرد نصب را می توان پس از راه اندازی سیستم بررسی و تنظیم کرد.
نظارت
در طول نظارت بر سیستم، اندازه گیری جریان، فشار و هدایت آب انجام می شود. برای بررسی اثرپذیری هیدرولیکی سیستم، فشار تغذیه در هر مرحله و جریان نفوذی باید اندازهگیری شود. فشار تغذیه بستگی به دمای آب تغذیه دارد. هنگامی که دمای آب خوراک پایین است، فشار بیشتری برای دستیابی به همان بازیابی مورد نیاز است که در هنگام بالا بودن دمای آب خوراک حاصل می شود. زمانی که دمای آب در نوسان است، باید جریان تراوش را عادی کرد تا بتوان با وضعیت شروع مقایسه کرد.
هنگامی که تاسیسات به درستی کار می کنند، رسانایی تراوا کم است، به دلیل حذف یون های یک ظرفیتی و دو ظرفیتی. زمانی که یک نشتی در عنصر غشا قرار می گیرد، رسانایی افزایش می یابد. به همین دلیل است که اندازه گیری ها اعمال می شود.
این اندازه گیری ها در زهکشی جمع آوری تراوش انجام می شود. اندازه گیری ها را می توان برای هر پشته مجزا یا برای همه پشته های موجود انجام داد.
نظارت کافی بر سیستم، کاربر را قادر می سازد تا بداند چه زمانی سیستم نیاز به تمیز کردن دارد.
حفاظت از مواد
در تاسیسات نمکزدایی، زمانی که صحبت از خوردگی بخشهای مختلف سیستم میشود، یک محیط طبیعی وجود دارد. به همین دلیل، ماده باید مقاومت خاصی در برابر خوردگی داشته باشد. این برای قطعات خارجی که در معرض منابع نمکی قرار دارند .و همچنین برای قطعات داخلی صدق می کند. معمولاً می توان مانع از خوردگی قطعات خارجی سیستم با تامین یک لایه سطحی(رنگ آمیزی-گالوانیزه کردن) شد.
علیرغم اینکه مواد در برابر خوردگی بالقوه محافظت می شوند، باید در برابر فشار، ارتعاشات و دماهای متغیر نیز مقاوم باشند.
برای جلوگیری از خوردگی و واکنش های شیمیایی در قسمتی از سیستم که فشار کم (<10 بار) است، مانند عناصر غشایی و مخازن تحت فشار، اغلب از غیر فلزات مانند PVC و فایبرگلاس استفاده می شود. برای قطعات پرفشار (۱۰ تا ۷۰ بار)، مانند پمپ ها، زهکش ها و درب ها، باید از فلزات استفاده کرد تا از همان نوع محافظت برای آنها استفاده شود.
جنس تجهیزات آب شیرین کن
پی وی سی و برخی فلزات نمی توانند به اندازه کافی در برابر خوردگی مقاومت کنند.
ماده اصلی که برای قطعات پرفشار استفاده می شود فولاد ضد زنگ است. مزیت فولاد ضد زنگ این است که در برابر خوردگی و خوردگی فرسایش مقاوم است. فولاد ضد زنگ به ندرت توسط خوردگی گالوانیکی آسیب میبیند.
تجهیزات نصب شده معمولاً از مواد زیر ساخته می شوند :
فیلترهای شمع و مخزن تحت فشار: فیلتر پلی پروپیلن در ظرف PVC یا فولاد ضد زنگ
پمپ: فولاد ضد زنگ
لوله های کم فشار: PVC
لوله های فشار بالا: فولاد ضد زنگ
سیستم تمیز کردن: PVC یا سایر مواد مصنوعی مقاوم در برابر مواد شیمیایی